Секрети якості насіння Biligrain: принципи вирощування та доробки насіннєвого матеріалу
Перелічуючи чинники, що впливають на майбутній урожай, завжди насамперед вказують якість насіння. Бо саме в малій насінині зберігається той генетичний потенціал, який заклали у сорт чи гібрид селекціонери. Далі, у товарному посіві, «втілення» цих властивостей залежить від умов та майстерності агронома. Але спершу до його рук має потрапити насіння, яке виростили та підготували спеціально для цієї мети. А цей процес потребує особливих підходів. Ми дізнались, як на Хмельниччині, у ТОВ «АГРОКРАЙ» вирощують та створюють якісний посівний матеріал бренду Biligrain.
Поле: у пріоритеті — пожива
«Точкою відліку» для насінини є поле. Як зауважив Василь Косюк, головний агроном підприємства, в нинішніх непростих умовах вирощувати сільськогосподарські культури загалом стало складніше. А виплекати насіннєві посіви — тим більше. Однак господарство обрало для себе певні принципи, які дають змогу завжди досягати потрібної якості врожаю.
Зокрема:
- Рослина має отримати всі необхідні поживні речовини в потрібній кількості, в потрібний час.
- Впровадження точного землеробства дає змогу надати рослині всю поживу й підвищити ефективність вирощування.
- Піклування про родючість ґрунту завдяки відповідним системам його обробітку та застосуванню сидератних технологій.
- Збереження вологи у ґрунті усіма можливими способами.
Як працюють ці та інші принципи, ми переконались безпосередньо в полях — спостерігаючи за збиранням озимої пшениці. Цьогоріч в господарстві на насіння сіяли 4 сорти цієї культури — КВС Ронін, КВС Еміль (KWS), Фелікс та Катаріна (Saaten Union).
«Це нові сорти, пристосовані до тих посушливих умов, які останнім часом спостерігаються навіть у нашій зоні, яка традиційно вважалася зоною з достатнім зволоженням. До того ж це сорти ранньо- та середньостиглі. Ми звернули увагу саме на них, бо вони встигають використати зимові запаси вологи. Завдяки чому ці сорти можуть підходити і для більш південних регіонів. Зараз саме ранньостиглі посухостійкі сорти найбільше потрібні аграріям, адже в останні 7 років ми бачимо тенденцію, що стає сухіше, запас ґрунтової вологи падає. Й основним лімітуючим фактором, особливо в останні 2 роки, є саме волога», — пояснює Василь Косюк.
Задля впровадження системи точного землеробства в компанії оновили технічний парк і тепер, починаючи від розкидачів добрив і до сівалок, — усе пристосовано для цієї мети. Крім того, систему живлення застосовують відповідно до результатів аналізу ґрунту, який проводять відразу після збирання попередника.
«Ми співпрацюємо з компанією, що розробила власну схему аналізу і систему відбору зразків. Зараз в Україні найчастіше використовують методику, за якою поля «сіткуються» на однакові квадрати по 2-5 га, і ґрунт на аналіз відбирається по цих квадратах. Натомість ми вибрали іншу методику — поле ділиться за ґрунтовими відмінами. Тобто накладаються багаторічні карти досліджень полів і створюється схема ґрунтових відмін, залежно від рельєфу, типу ґрунту, породи нижніх шарів тощо. По цих ґрунтових відмінах і відбираються зразки. Тобто якщо це схил, то відбирається зразок на схилах, так само і на горбках та в низинах. Бо там зазвичай різні показники по елементах живлення», — каже головний агроном.
Такий вибір мотивований, зокрема, і тим, що у Красилівському районі Хмельницької області, де розташовані землі «Агрокраю», рельєф переважно горбкуватий. Хоча саме насіннєві посіви тут намагаються розміщувати на більш рівнинних площах.
На основі отриманих результатів аналізів ґрунту розробляються карти живлення, вони інтегруються в систему диференційованого внесення і далі техніка працює за цією системою.
Наприклад, на запланований урожай під 8 т/га пшениці раніше розраховували середні норми: 80 кг/га фосфору в д.р., 90 кг/га калію. Азоту під основне осіннє внесення 30-50 кг/га. А потім ще 3 весняні підживлення, загалом 140-160 кг/га азоту в д.р. Зараз на підставі ґрунтових відмін на різних ділянках норми можуть серйозно коливатися. Наприклад, у низинах, де є намиті ґрунти і накопичуються поживні елементи, фосфору можуть давати не більше 30 кг/га. А на горбках — і по 120-130 кг/га д.р. фосфору.
«Диференційоване внесення мінеральних добрив і диференційований посів — один із головних факторів, які забезпечують вирощування насіння найвищої якості. Завдяки впроваджуваним технологіям наше насіння може вирости здоровим, вирівняним в енергії, і розкрити надалі свій генетичний потенціал», — переконаний Олег Білявець, керівник ТОВ «Агрокрай».
А Василь Косюк, головний агроном підприємства, поділився із нами ще деякими секретами вирощування високоякісного насіннєвого матеріалу.
- Обробка насіння озимої пшениці перед сівбою рідким фосфором і цинком — вдалий прийом в умовах нестачі вологи. Завдяки цьому коренева система загалом значно краще розвивається, а вторинна розвивається швидше. Таким чином краще відбувається відновлення вегетації навесні й вона встигає вхопити зимову вологу.
- Використання для захисту насіннєвих посівів лише оригінальних препаратів, причому з акцентом на профілактику.
- Застосування органіки. Готуючи ґрунт під сівбу, рівномірно розподіляють рештки попередника на полі, вносять біодеструктор і відразу сіють сидерати — зазвичай це гірчиця, олійна редька, під певні культури можуть додавати ще й бобові.
- Збирання врожаю відбувається комбайнами-гібридами. Тобто вони оснащені і ротором, і барабаном. Більш того. Комбайни, які застосовують в «Агрокраї», переобладнані і мають 3 барабани й один ротор. Завдяки чому, за словами головного агронома, вони, по-перше, добре вимолочують. А по-друге, роблять це досить ніжно й акуратно.
- Зерно із бункера засипається спочатку в перевантажники, які потім доставляють його до машин, що чекають на краю поля. Особливість цих перевантажників у тому, що вони не мають шнеків, і зерно м’яко «стікає» у вантажівку мінімально травмуючись при цьому.
Намилувавшись роботою комбайнів, що жнивували пшеницю, ми поспішили разом з машинами, навантаженими щойно зібраним зерном, далі — на власний насіннєвий завод компанії, який виробляє насіння під брендом Biligrain.
Завод: на лінії удосконалення
Новий сучасний завод і розміщений поруч креативний офіс компанії Biligrain вразили нас із першого погляду. Про історію його створення розповів засновник і директор Олег Білявець. Ідея щодо відкриття насіннєвого заводу зародилася у пана Олега та його батька ще у 2014 році. На той час вони вже протягом 10 років займалися рослинництвом і розуміли потреби аграріїв щодо якісного посівного матеріалу прибуткових культур. Від ідеї до її втілення пройшло 5 років. І у 2019 завод запустили в тестовому режимі, а з 2020 він уже працює на повну потужність.
«Але спочатку, упродовж 2 років ми відвідували десятки заводів Європи, зокрема, Німеччини. Вивчали їхні технології, аналізували ринок. Вже тоді ми вирішили для себе, що проект і обладнання має робити саме професійна європейська, а то і світова компанія. Зупинилися на німецьких професіоналах. Запросили всесвітньо відомого інженера в цій галузі Гьорга Рейтера. Він приїздив сюди і розробив спеціально для нас модель заводу та технологію виробництва насіння», — поділився Олег Білявець.
За його словами, завод сконструйований так, що фактично кожна насінина дбайливо і ніжно «проводиться» по всьому шляху — від завантажувальної ями до упаковки, через усі транспортні механізми та очисне обладнання.
Тож і в доробці насіння для компанії є основні принципи:
- «м’яке» транспортування,
- дбайлива обробка,
- точне калібрування,
- максимальне очищення,
- безпека на всіх етапах.
І ми мали змогу подивитися, як реалізуються ці принципи, та відслідкувати шлях зерна на екскурсії заводом, яку провів для нас завідувач виробництва Віктор Котік. Звісно, спочатку ми зайшли у приміщення, де працівники перевдягаються в робочу форму, адже техніка безпеки — беззаперечний пріоритет. Тож будь-хто, навіть «сторонні журналісти», переступивши поріг заводу, повинні вдягнути захисні каски та люмінесцентні жилети.
Отже, екіпірувавшись, ми вирушили у «приймальне відділення», тобто в завальну яму, звідки зерно подається стрічковими гумовими транспортерами до першої машини, з якої починається очищення. Цією машиною є магнітний сепаратор. Він «виловлює» металеві частинки, які можуть опинитися в масиві зерна після комбайнування і транспортування. Загалом, за словами завідувача виробництва, таких сепараторів на заводі 4, що максимально убезпечує кінцевий продукт від небажаних домішок, особливо якщо це стосується продукції, призначеної для харчових цілей.
Зазначимо, що усі норії завальної ями — підвісні, резинові, що виключає травмування зерна вже із найперших етапів роботи із ним. До речі, яма також спроектована самим Гьоргом Рейтером, і побудована таким чином, що вивантажене зерно м’яко стікає донизу, бо бункер і транспортер перебувають у «підвішеному» стані, на спеціальних кріпленнях, а не зафіксовані на нижніх підпорках.
Тут іще важливо зауважити, що на всіх ділянках виробництва, починаючи із завальної ями, встановлене спеціальне обладнання, яке утворює систему аспірації повітря на заводі.
«Коли зерно рухається, то піднімається і розповсюджується пил — і той, що в полі накопичився, і з часточок зернових оболонок. У нас на кожній машині, на кожній ділянці транспортерів на вході і виході стоять аераційні колонки. Вони витягують цей пил і подають на фільтри — один дрібнодисперсний, що забирає пил із лінії попереднього очищення, а другий фільтрує пил із насіннєвої лінії. Більше того, на опірних постах на всіх ділянках розміщені шланги і пістолети з повітрям, й у певних місцях — технологічні пилососи. З їх допомогою ми очищуємо всі лінії і машини після кожної культури, щоб не було змішування сортів і культур», — зауважив Віктор Котік.
І далі завідувач виробництва повів нас у «мозковий центр» заводу — операторську. Звідси можна запустити чи зупинити виробничу лінію лише порухом комп’ютерної мишки. Як розповів Юрій Квілінський, керівник зміни, сюди із датчиків, встановлених на всьому обладнанні, надходять дані, відповідна програма їх обробляє й оператор може слідкувати за усім, що відбувається на кожному етапі. А в разі виникнення якихось проблем програма усуває їх автоматично, або ж сигналізує і сам оператор чи відповідний працівник розбираються з ситуацією.
«Машини запускаються за допомогою мишки і клавіатури. Оператор будує маршрути, якими має рухатися зерно. Далі процес іде автоматично за заданим маршрутом. Окрім датчиків, які відслідковують роботу агрегатів (наприклад, датчики підпору, швидкості, сходу стрічки, рівнів бункерів тощо), є ще камери, що подають зображення на екран монітора. Оператор може безпосередньо бачити, що відбувається на ділянках, які потребують більшої уваги», — уточнює Віктор Котік.
Завдяки системі автоматизації процесів втручання людини в них — мінімальне. Тому на зміні зазвичай працюють лише 4 співробітники.
Загалом виробництво на заводі складається із 2 ліній очищення. На першій, первинній лінії забираються крупні і дрібніші домішки. На вторинній лінії відбувається калібрування і відбір за питомою вагою, формується маса 1000, здійснюється протруювання.
Насамперед ми поспостерігали, як працює універсальна зерноочисна машина первинної обробки МУЗ-16. За словами Віктора Котіка, вона здатна обробляти 100 т/год. товарного зерна і 40 т/год. насіннєвого зерна. Аби побачити роботу цієї машини, нам знадобилося піднятись на другий ярус очисної лінії. Ще вище, на третьому ярусі лінії первинного очищення, працював роторний сепаратор MGP-100, де скапілятор забирав як грубі рештки, так і дрібні домішки. Саме на нього спершу потрапляє зерно після завальної ями і потім іде вниз, на МУЗ-16.
Аби ми не втомились від бігання по багатоярусних сходах, Віктор Котік попрямував далі вгору і «відчинив нам двері у світ» — майже під дахом виявився вихід до галереї із зовнішніми транспортерами закритого типу. Одним зерно із завальної ями подається на очисні лінії, а другим, у зворотному напрямку, вже готове товарне зерно подається на пункт відвантаження. З галереї ми мали змогу у всій красі побачити сушарку.
«Наша сушарка Reala має перевагу в тому, що може сушити в низьких температурних режимах, що дуже важливо для насіння. Ми можемо підсушувати його в режимі 30-40 0С. За таких умов зародки зберігаються краще», — розповів завідувач виробництва.
Намилувавшись з висоти величною сушаркою та краєвидами полів і вишневим садком підприємства, розташованим поруч із заводом, ми продовжили вивчати «шлях зерна», — спустилися вниз і зазирнули на склад тимчасового зберігання. Тут після очищення на першій лінії зерно очікує на подальше «вдосконалення» на другій лінії. А також на результати аналізів, які проводять фахівці лабораторії, розміщеної тут же на заводі. Визначаються основні параметри кожної партії і відповідно режими, за якими потім зерно дороблятимуть.
Сам склад також організований так, щоб зберегти якісні характеристики насіння.
«Цей склад розподілений на «комірки» і ряди, таким чином виключаються помилки в розмежуванні посівного матеріалу та сортів/гібридів. Зберігається насіння в контейнерах, виготовлених із сухого дерева, завдяки чому навіть якщо вологість засипаного в них зерна дещо підвищена, надалі вона не зростає, зерно не «париться», — пояснив Віктор Котік.
Наступний етап — друга лінія очищення. На заводі кожен крок і процес продуманий до дрібниць. Наприклад, навіть доставка зерна в контейнерах зі складу і завантаження його в бункер очисної лінії.
«Є заявка, водій телескопічного фронтального навантажувача під’їжджає, сканером знімає штрих-код, розуміє, що це той контейнер, який йому потрібен, і далі відправляє його в бункер на доочищення. Причому на навантажувачах встановлена система «Ротатор», яка дає змогу перевернути контейнер на 360 градусів, тож усе зерно із нього легко висипається, нічого не залишається в контейнері», — роз’яснив пан Віктор.
До слова, під час пересипання ми не помітили ні «хмаринки» пилу, — так наочно можна було переконатися, що система аспірації працює ефективно.
Отже, з бункера по норії зерно вирушило до наступного етапу очищення і ми попрямували за ним, для чого піднялись на другий поверх очисної лінії.
Тут на зерно чекає калібрування на машині Fine Cleaner FP 1000 (Westrup), яка має 2 блоки по 2 решітні стани. Завдяки «перетрушуванню» на на цих станах, зерно від зерна відділяються дрібні і «неформатні» фракції і формується необхідна однорідно крупна.
«Тут встановлені решета, якими можна відібрати короткі за розміром зерна. При цьому відбувається ще й доочищення — згаданою системою аспірації «витягуються» легкі домішки. Водночас те, що менше за поставлений на решеті діаметр, іде у придатні відходи — тобто таке зерно можна використати як корм у тваринництві чи для інших потреб», — пояснив роботу агрегата Віктор Котік.
Далі вже сформований за розміром продукт піднімається по норії і подається на трієрний блок. У ньому є 2 циліндри, які відбирають коротку та довгу домішку від основного продукту. Частоту обертання циліндрів можна регулювати, завдяки чому машина може працювати з різними культурами.
Із трієрного блоку, розміщеного на 3-му поверсі, зерно спускається поверхом нижче — на гравітаційний стіл. Біля нього ми, що називається, «залипли». Цю машину ще називають «киплячим столом», бо зерно у ньому схоже на кашу, яка кипить і «булькає», і всі легкі домішки піднімаються вгору й переміщуються по «схилу» стола, який розташований під невеликим кутом. Таким чином виводиться у відходи непридатне на насіння зерно — воно легке, невиповнене, невимолочене або заражене хворобами, передусім фузаріозом.
Натомість велике, виповнене, здорове і відкаліброване виводиться на іншу норію. Зачерпнувши по жменьці зерно із двох потоків ми могли наочно побачити різницю — де «брак», а де потенційний урожай на полі. Так діють закони фізики: здавалося б, простий процес — розтрушування під нахилом, а зернова маса чітко розподіляється на потоки зерен із відповідним розміром і масою 1000. Звісно, щоб ці закони діяли, потрібне правильно налаштоване і надійне обладнання.
До слова, якщо насіння круглої форми (горох, ріпак), воно проходить додатковий «відбір» на спіральному сепараторі Westrup, за допомогою якого відсіюється пласке від круглого.
«Westrup — одні з небагатьох, хто залишив у своїх лініях такі машини. Працюють вони так: відкривається клапан, зерно сиплеться зверху на такі собі резинові спіралі. За законами фізики круглі форми, центруючись, продовжують скочуватися по спіралі донизу, а пласкі на певному етапі вилітають назовні. До речі, цю машину в народі називають «Попелюшкою» — вона теж перебирає зерно за формою, як героїня відомої казки», — зауважив Віктор Котік.
Він зауважив, що далі кругле відібране зерно зі спірального сепаратора знову надходить на гравітаційний стіл і ще раз калібрується.
А далі пан віктор підвів нас до ще однієї машини, яка виконує досить важливу функцію. Це був каменевідбірник Bühler. Як зауважив наш «екскурсовод», зазвичай вітчизняні виробники на машинах, що виконують цю функцію, трохи економлять. У Biligrain вирішили підійти скрупульозно й обрали саме цей якісний швейцарський бренд. Агрегат «відсіває» органічні домішки, грудочки землі, каміння, а також скло. До речі, скло жодна інша машина не може відібрати — воно і не магнітиться, і повітрям не видувається. Відбір таких домішок особливо необхідний, коли очищається харчовий продукт. Наприклад, квасоля, яку в «Агрокраї» вирощують і реалізують також.
Фінальний етап калібрування й очищення насіння — фотосепаратор Bühler DA MultiVision. Унікальна машина, яку можуть дозволити собі не всі насіннєві заводи.
«Тут стоять 24 оптичні камери, які фіксують візуальні ознаки й за рахунок чого йде відбір насіння за відтінком кольору, пігментними плямами, дефектами тощо. Машина обладнана 256 повітряними інжекторами, що пов’язані з камерами. Камера бачить, а інжектор відбиває зерно за відповідними параметрами. У цій машині ще є потрійне доочищення. Вона обладнана 2-ма бункерами. Основний продукт потрапляє в один бункер (розподілившись на 3 лотки) й очищається за допомогою інжекторів і камер. Якщо ж машина «сумнівається», то кидає зерно ще на рециркуляцію, тобто в другий бункер, де насіння знову проходить етап доочищення. Таким чином відбирається найкраще зерно. Решта йде у відходи», — пояснив роботу фотосепаратора Віктор Котік.
Нарешті зерно очищене й відкаліброване. По суті, цей етап завершено. Але на третьому поверсі розміщено обладнання для ще одного важливого процесу. А саме — протруювання насіння. Це, за словами завідувача виробництва, — окрема зона, яка умовно відмежована «червоною лінією». Тобто у різний спосіб відділена від інших. Тож тут, на верхньому «ярусі», обладнання, що стосується лінії протруювання, міститься в окремій «кабінці». На дверях якої, звісно ж, написано «Стороннім вхід заборонено». Але для нас зробили виняток і дозволили зазирнути всередину.
У невеликому приміщенні ми побачили 2 агрегати. Один виявився фільтром системи аспірації, яка окремо очищує лінію протруювання. Очищене повітря викидається назовні, а те, що зібрано фільтром, відправляється в герметизований контейнер і потім утилізується.
Другий агрегат — порційний протруювач Willy Niklas. Обробляє насіння за методом наважування. Порція дозується, подається в центрифугу, де зерно розкручується, і спеціальні лопатки перемішують зерно, задаючи йому «правильне» перевертання, відповідно до встановленої рецептури. Таким чином кожна насінина рівномірно і в потрібній кількості «огортається» протруювачем. Потужність машини — 8-10 т/год. Також, за словами Віктора Котіка, цей агрегат дає можливість наносити порошкові препарати.
«Дуже класна система. Мені особисто подобається тим, що всі процеси з самого початку, зі змішування емульсії, води з препаратами — все на вагах. Далі перекачується в насоси — теж на вагах. Тобто весь цей процес система «бачить» у грамах. Що дає точність нанесення і дозування порції», — пояснив він.
Далі вже готова продукція по резиновому транспортеру йде на дільницю фасування.
Ми думали, що третій поверх — це вже найвища точка і більше не доведеться підніматися сходами, але де там!
Невгамовний Віктор Котік попрямував іще вище — по драбині під самий дах. І там показав установку, де відбувається перемикання-перенаправлення маршрутів зерна за допомогою 2- і 3-ходових клапанів. Вона дає змогу легко будувати технологічні маршрути для певної культури й для певних завдань.
А поряд верхівка Z-норії, яка кладе зерно у бункер на «фінальному виході».
З цієї найвищої точки, де було трохи спекотно, ми спустилися вниз, і оглянули ще одну, окрему дільницю калібрування, що розділяє зерно на 4 фракції, а також ближче познайомились із принципом дії Z-норії, яка доставляє зерно у бункери.
«Z-норія — найбільш дбайлива, вона доносить зерно без травмування. Працює вона так: за допомогою барабана відбувається чітке дозування порції і вона кладеться в ковшик. Самі ковшики вільно закріплені на вісях і тому на «поворотах» залишаються в горизонтальному положенні й «амортизують». Плавно піднімаються вгору і бережно висипають зерно в бункер», — пояснив Віктор Котік.
Цей бункер розділений на 4 частини — для кожного калібру окремо. Що, коли і куди засипати — рішення може приймати як поператор, так і безпосередньо на місці водій навантажувача, який може натиском кнопки вивантажити продукт певного калібру в потрібний контейнер. Цю окрему дільницю калібрування зазвичай використовують для доробки бобових культур, кукурудзи, соняшнику.
Екскурсія продовжувалась, і ми мали змогу детальніше роздивитись «перший поверх» лінії очищення, відповідні етапи якої проходили на верхніх ярусах.
Насамперед Віктор Котік показав нам автоматичні й напівавтоматичні пробовідбірники марки Cimbria. На них виставляється кількість проб та період, через який вони відбираються (5-10 хв.). Кожна проба потім аналізується в лабораторії, перевіряється на якість. Якщо це продукт стороннього замовника, усі дані заносяться у спеціальну програму і власник може побачити їх онлайн, слідкуючи за тим, що ж відбувається з його насінням в реальному часі.
Також тут працювали іще дві Z-норії, які вже на кінцевому етапі доправляли насіння до дільниці упаковки. З однією із них сполучена невелика протруювальна установка, призначена для тих випадків, коли потрібно обробити невелику партію зерна. А поряд — окреме приміщення першого поверху зони протруювання, верхній ярус якого ми оглядали раніше. Таємничі двері з обмежувальною табличкою для нас знову відкрили і ми потрапили туди, де готуються розчини й емульсії. Побачили там 2 контейнери. В одному з них, за словами завідувача виробництва, була привозна вода, і в разі потреби тут коригують її кислотність. А у другому — відходи, що залишаються від промивання системи протруювання. Надалі їх утилізує спеціалізована компанія, з якою підприємство уклало договір.
Тут же стоїть міксер — елемент протруювальної системи Willy Nicklas — куди, з чітким дозуванням буквально до грама, подається препарат та вода й ретельно перемішуються. А далі насоси на тензодатчиках подають потрібні порції суміші до агрегату на третьому поверсі, де й відбувається протруювання насіння.
Нарешті — останній етап: дільниця фасування. Тут є можливість фасувати готову продукцію як у картонні мішки, так і у великі біг-беги. Причому окремо розмежовані дільниці для пакування протруєного зерна та непротруєного.
Тут ми побачили вже партію розфасованого насіння пшениці сорту Катаріна під брендом Biligrain, готову до відправки замовнику.
Як зауважив, підсумовуючи нашу екскурсію, Віктор Котік, завод розрахований на випуск до 240 т насіння на добу. Ми потрапили сюди саме в сезон збирання озимої пшениці, але, як бачимо, обладнання пристосоване для обробки насіння найрізноманітніших культур, будь-яких фракцій і калібрів. І ці можливості підприємство використовує сповна, адже в «Агрокраї» вирощують і сою, і кукурудзу та інші основні культури, а також і нішеві, зокрема, мак і розторопшу.
До слова, наразі Biligrain крім насіння згаданої озимої пшениці сортів КВС Ронін, КВС Еміль (KWS), Фелікс та Катаріна (Saaten Union), також планує до реалізації сою сортів Асука, Аріса (Prograin), Кардифф та СГ Кеа (Saatbau). І 3 сорти квасолі — СН-1 Мерлін біла мала (Merlin Navy Beans), СН-1 Зорро чорна мала (Zorro Black Beans) та СН-1 Монткалм червона велика (Montcalm Dark Red Kidney). У найближчому майбутньому асортимент поповниться ячменем, спельтою й амарантом.
Наш день в гостях у Biligrain був і справді насиченим. Нам вдалося і на жнивах побувати, і пройти детальну екскурсію насіннєвим заводом, а ще — поласувати смачною продукцією пекарні «Мамин хліб» та познайомитися із професіоналами, що захоплюються своєю справою, і змогли у невеликому селі на Хмельниччині створити сучасне інноваційне виробництво з упевненістю в перспективу. Гарний взірець для вітчизняного насінництва.
©Алла Гусарова, Тетяна Шмігель, SuperAgronom.com, 2020 р.
Думка редакції SuperAgronom.com може не збігатися з точкою зору автора. Редакція не несе відповідальності за достовірність і тлумачення наведеної інформації і виконує роль виключно носія.
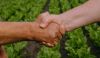
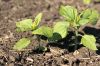
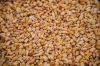
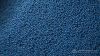